ME153 Vine-Saber
March - May 2023
Context:
The ME153 Junior Design had me working in a team of 4 on a design project for 5-weeks. Our team chose to work on improving toy lightsabers and made the Vine-Saber.
Skills:
-
Pneumatics
-
Electronic design
-
Rapid Prototyping

Goal:
We aimed to improve toy lightsabers that are currently on the market. Toy lightsabers currently lack automatic blade retraction, breaking the immersion of users when they have to manually retract their lightsabers. Our proposed solution was to use an inflated vine robot as the saber-blade which can fully extend and retract at the push of a button. This solution would address the lack of retraction while having the added benefit of being soft-bodied and safe when hitting others with the blade.


Prototyping:
We made a total of 5 prototypes, one for each week we had to work on the project. Prototype 1 addressed pressurization and retraction methods. Prototype 2 formed the pressure sensing, airtight hilt, and vine-body spooling. Prototype 3 moved away from pressure control and into pre-pressurization while still trying to solve the buckling of the fabric blade. In prototype 4, we finalized the electronics, our pressure modeling, and identified our motor requirements. Prototype 5 integrated all the components together while adding a clutch mechanism for the spool.
What I specifically worked on:
-
Prototype brainstorming sketches
-
Experimenting with tape measures and clock springs
-
Making the first airtight hilt
-
Soldering the protoboard
-
Fine-tuning the spool clutch and adding a spring
-
Creating an airtight mechanical button for the clutch
-
Making the final fabric blade which solved buckling on retraction
-
Pressure data smoothing and analysis
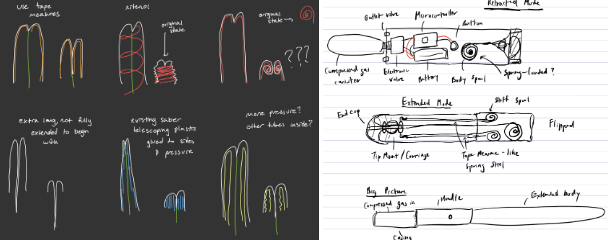


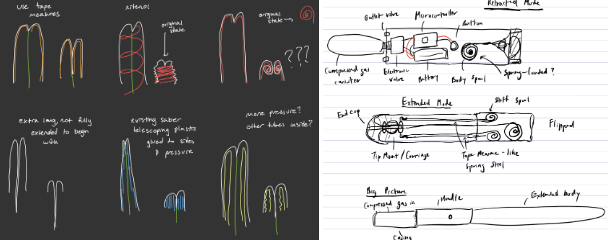
Final Prototype:
Our final prototype added finishing touches to the project for the design poster fair. This includes adding an LGB LED light and changing the blade fabric and shape. The hilt was spray-painted and 3D prints were used to hide glue and protect critical user interfaces.




Takeaways:
-
In the poster competition competing with 22 other groups at the end of the quarter, our project team received 'Best Overall' with the rankings based on innovation, marketability, technical, and presentation.
-
We did not expect the buckling of the fabric body to me such an issue and should have committed more time to solving it earlier than we did. This would have helped us realize how much pressure and how strong of a motor we needed earlier.
-
Practiced rapid prototyping, root cause analysis, and providing elevator pitches
-
For further prototyping of this project, we could improve our motor or make a smaller and more airtight hilt. We could also add a built-in hand pump and an LED string. The clutch-button can be refined and made more robust.
-
The use of clock springs and measuring tapes could also have worked with more testing